Commercial Roof Maintenance Inspections in Eden Prairie
Commercial Roof Maintenance Inspections in Eden Prairie
Maintaining the health of a commercial roof in Eden Prairie is essential to protect a business from unexpected expenses and disruptions. Regular roof maintenance inspections can pinpoint issues before they turn into costly repairs, ensuring smooth operations. Identifying potential problems early saves both time and money, keeping a commercial property in top shape.
At Allweather Roof, we understand that a thorough inspection not only checks for visible damage but also assesses the underlying issues that might not be immediately noticeable. This involves examining the roof materials, checking for water damage, and ensuring proper drainage. By doing this, we help businesses maintain the integrity of their roofs and extend their lifespan.

Essential Key Takeaways for Commercial Roof Maintenance Inspections
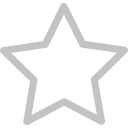
Regular inspections detect hidden roof issues early.
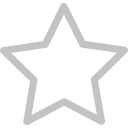
Thorough assessments prevent unexpected expenses.
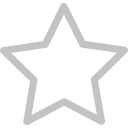
Scheduled maintenance extends roof lifespan.
Assessing the Need for Roof Inspections
Regular roof inspections are essential for maintaining the health and longevity of commercial buildings. By identifying potential issues early, we can prevent costly repairs and extend the roof’s lifespan.
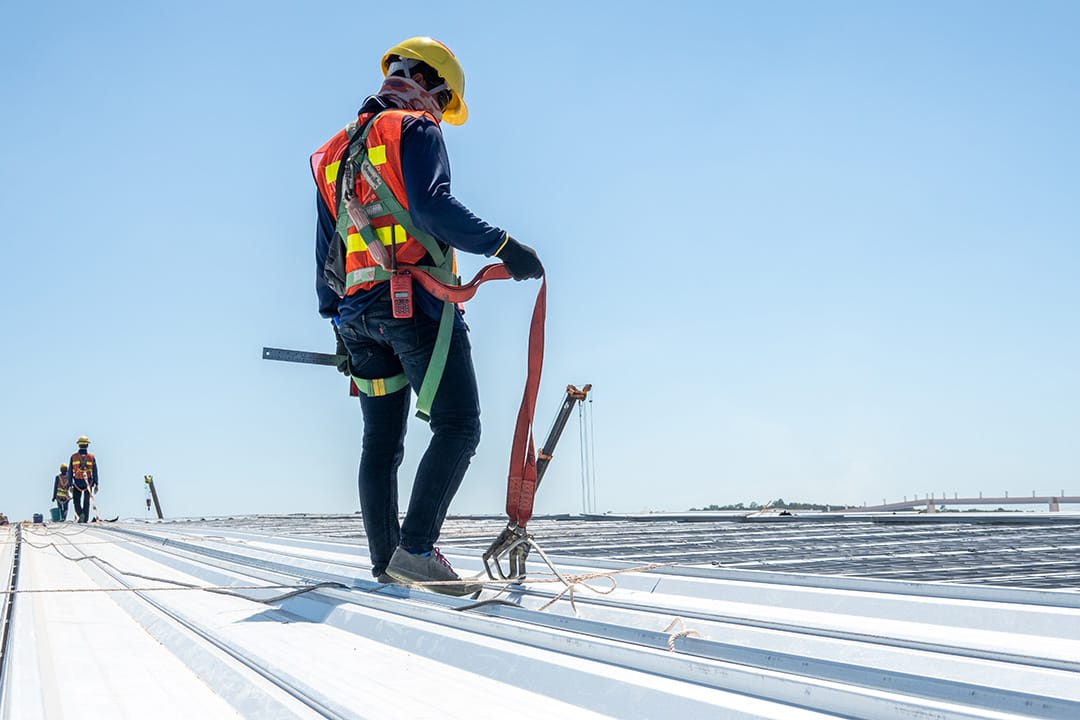
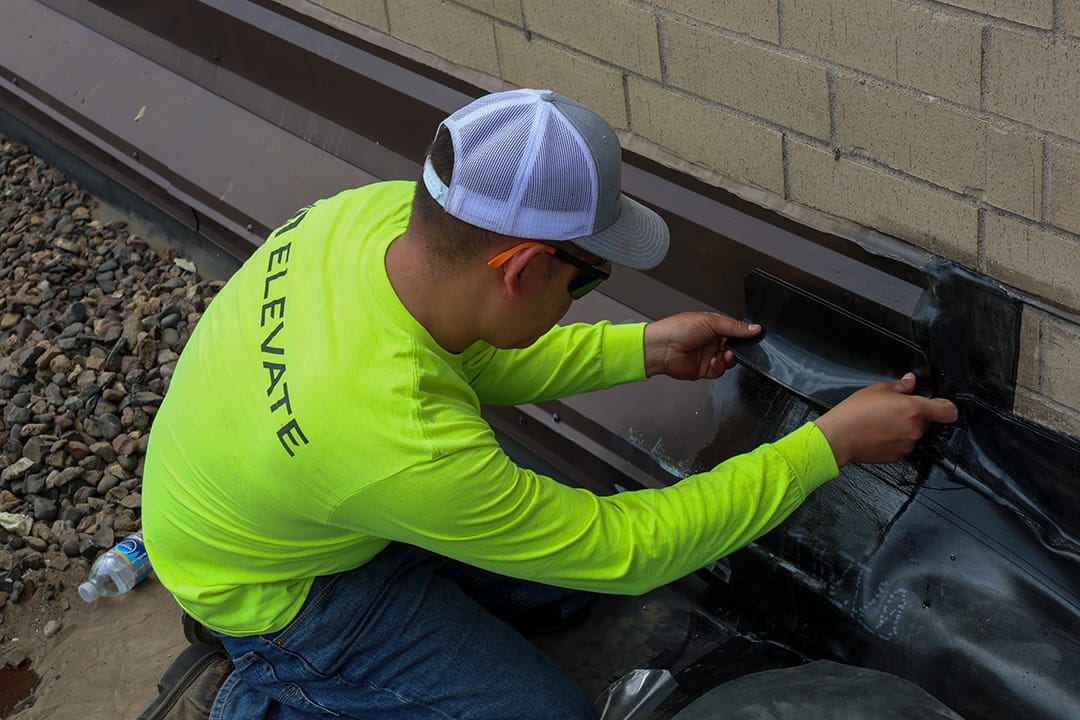
The Importance of Regular Maintenance
Maintaining a schedule for regular roof inspections allows us to spot wear and tear that might not be immediately visible. Over time, weather elements like rain, wind, and snow can degrade roofing materials. Regular checks help us address small issues before they become major problems, saving us time and money.
Routine inspections also ensure that roofs remain compliant with building codes and regulations. In Eden Prairie, adhering to the required standards helps us avoid penalties and ensures the safety and efficiency of our buildings. Regular maintenance is a proactive step in protecting our investment.
Identifying Potential Roof Issues Early
Catching roof issues early is crucial for preventing significant damage. Inspections can reveal problems such as leaks, mold, or structural weaknesses. Early detection means we can take action before these issues impact the interior of our building.
We can also use roof inspections to evaluate the effectiveness of previous repairs or installations. This process provides us with valuable insights into our roof’s current condition and helps plan any future maintenance efforts. By focusing on early identification, we optimize our approach to roof care and management, ensuring our buildings remain safe and sound.
Key Elements of a Roof Inspection
In commercial roof inspections, we focus on evaluating the surface and membrane, analyzing drainage systems and water flow, and inspecting insulation and underlayment. Each of these elements is crucial for the longevity and safety of the roof.
Surface and Membrane Evaluation
When we evaluate the roof’s surface and membrane, we start by checking for visible damage such as cracks, blisters, or punctures. These issues can lead to leaks, compromising the roof’s integrity. We also look for signs of wear and tear that might indicate that the roof has reached the end of its lifespan.
This evaluation includes checking for ponding water or any evidence that water is not draining properly. Materials matching the specified type must cover the entire surface. Proper adhesion and any visible seams must be verified.
We assess the membrane’s condition and ensure that there are no gaps or loose areas. By maintaining the membrane’s integrity, we help prevent water infiltration, which could cause serious damage to the building’s interior.
Drainage Systems and Water Flow Analysis
Proper drainage is vital in preventing water accumulation on a roof. We closely inspect gutters, downspouts, and internal drains to make sure there’s no blockage. Debris can cause water buildup, leading to leaks and structural damage.
We analyze water flow patterns to ensure efficient drainage, especially after heavy rainfalls. Verifying that water quickly exits through designated pathways reduces the risk of ponding.
Analyzing water flow also involves checking the slope of the roof. An appropriate slope helps direct water towards drainage systems effectively. Regular maintenance of these systems is important to keep the roof in top shape.
Insulation and Underlayment Inspection
During an inspection, we assess the insulation and underlayment for any signs of moisture damage or deterioration. Damp insulation can lead to mold growth and decreased energy efficiency in the building.
We check to see that the insulation provides sufficient thermal protection. Any gaps or settling in the insulation could mean higher heating and cooling costs for the building.
We also examine the underlayment to ensure it provides a robust barrier against water intrusion. Damage to the underlayment should be addressed promptly to maintain the protective layers of the roof. Proper insulation and underlayment support the roof’s long-term performance and efficiency.
Planning and Scheduling Inspections
When planning and scheduling inspections, key considerations include setting the right frequency and preparing for weather-related challenges. These steps help ensure timely maintenance and efficient management of commercial roofs in Eden Prairie.
Determining Inspection Frequency
Determining the frequency of inspections is essential for effective roof maintenance. Regular inspections, such as twice a year, are advisable for commercial roofs to identify minor issues before they escalate. Spring and autumn are ideal times because they follow seasonal changes.
Factors affecting inspection frequency include roof age, materials, and previous issues. Older roofs might need more frequent check-ups. Newer installations may permit a longer interval, although early inspections help verify proper installation. Usage and occupancy levels also play a role, allowing us to tailor the schedule to the building’s unique needs.
Preparing for Seasonal and Weather-Related Concerns
Preparing for seasonal conditions is crucial in Eden Prairie’s varied climate. We need to anticipate extreme weather such as snow, storms, and high temperatures. Winter inspections focus on snow load and ice damage, while spring checks are essential for identifying lingering moisture issues.
Summer inspections assess heat impact. It’s important to schedule inspections ahead of significant weather changes so that there is sufficient time to implement necessary repairs or reinforcements. Prioritizing vulnerable areas, like drainage systems and roof edges, can also prevent damage during heavy rainfall or snowmelt.
By being proactive, we minimize risks and ensure the roof remains in good condition year-round.

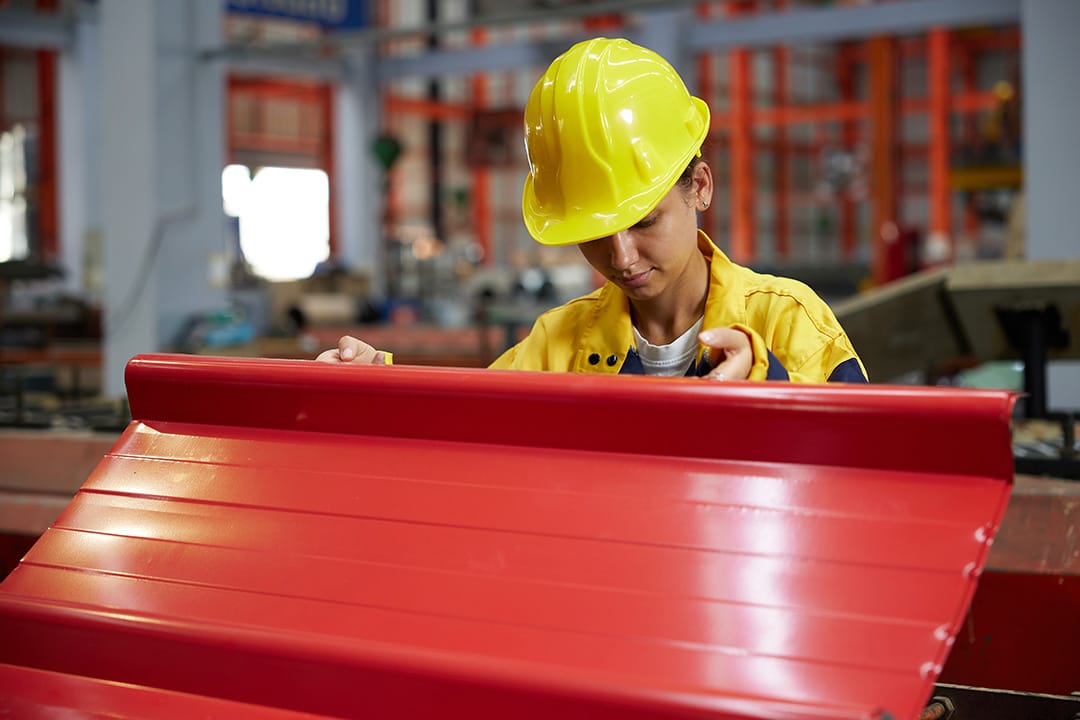
Executing the Inspection
When conducting a commercial roof inspection in Eden Prairie, we focus on ensuring the process is safe and effective. We prioritize safety protocols while using the right tools and technologies to identify potential issues.
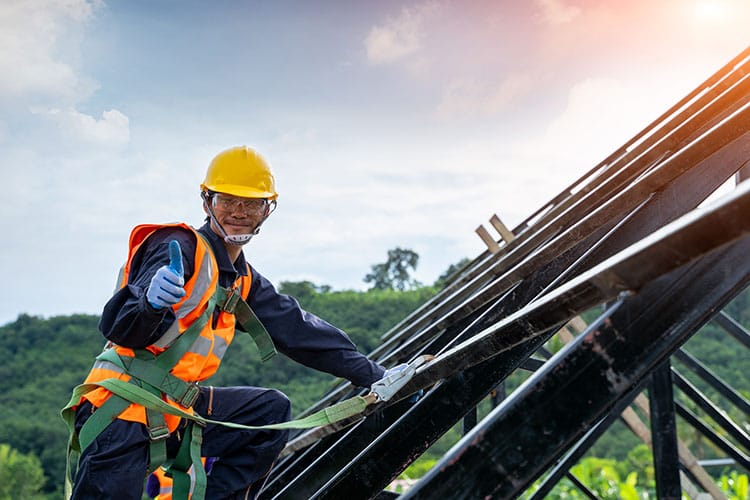
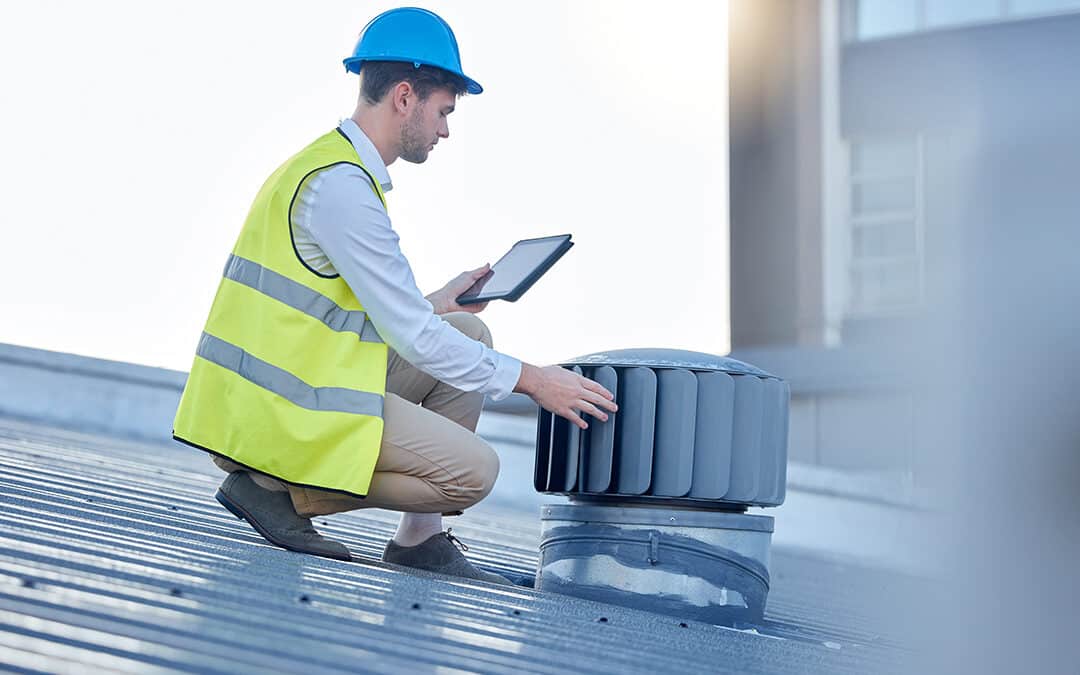
Safety Protocols and Procedures
Safety is essential during a roof inspection. We wear appropriate personal protective equipment (PPE) like helmets, gloves, and safety harnesses. This keeps us secure while navigating the roof.
Before starting, we check weather conditions. Rain or strong winds can create dangerous scenarios. We also assess the roof’s condition from the ground.
Communication is key. We use radios or phones to stay connected and report any immediate issues. This ensures everyone is informed and ready to respond if necessary.
Tools and Technologies in Inspection
We use a variety of tools and technologies to carry out efficient inspections. Drones help us get aerial views of large rooftops quickly. This helps identify any visible issues from above.
Infrared cameras detect heat loss or water leaks beneath the roof surface. These cameras provide accurate data without invasive methods.
For detailed inspection, we employ moisture meters. These measure moisture levels in insulation, indicating potential leak areas.
Ladders and scaffolds allow us to access hard-to-reach spots safely. Combined, these technologies ensure we gather comprehensive, reliable insights during the inspection process.
Post-Inspection Processes
After inspecting a commercial roof, we focus on two main tasks: compiling thorough reports and making clear maintenance recommendations. These help building owners understand their roof’s condition and plan necessary actions to maintain longevity.
Compiling Reports and Documentation
We start by organizing all findings into a detailed report. This includes photos of the roof, highlighting areas of concern such as leaks or damaged shingles. These images provide a visual reference and support our observations.
Next, we describe the condition of different roof components. Each section of the report explains observed problems and potential consequences. This information helps in assessing the severity and immediacy of required repairs.
Finally, we give a summary of all inspection activities, ensuring clarity and transparency. Our documentation becomes a valuable resource for managing the roof over time, laying a foundation for future inspections.
Maintenance Recommendations and Action Plans
Based on inspection outcomes, we develop specific maintenance recommendations. These might involve patching leaks, replacing damaged shingles, or conducting regular cleaning to prevent debris buildup.
We prioritize these recommendations to address urgent issues first, ensuring the roof remains functional and safe. Our action plans are laid out clearly with a timeline for each task.
By providing this guidance, we help building owners make informed decisions. The goal is not just repair but also preventive maintenance to extend the roof’s lifespan and avoid costly future problems. Regular updates on the progress of these actions ensure smooth and efficient implementation.